Fixing 3D Printing Stringing: Solutions and Techniques
In the pursuit of high-quality FDM 3D prints, overcoming challenges that affects quality is essential. One of the most common issues encountered is stringing, which can significantly detract from the finished object quality and surface finish.
What is stinging?
When the print head moves between different parts of a 3D print, the filament leaks or oozes from the nozzle, creating thin, hair-like lines. This is known as “stringing” and can occur when the extrusion process stops as the print head moves through empty spaces in the design. Stringing is caused by various factors, including filament moisture and temperature, retraction settings, printing speed, and the type of extrusion system being used.
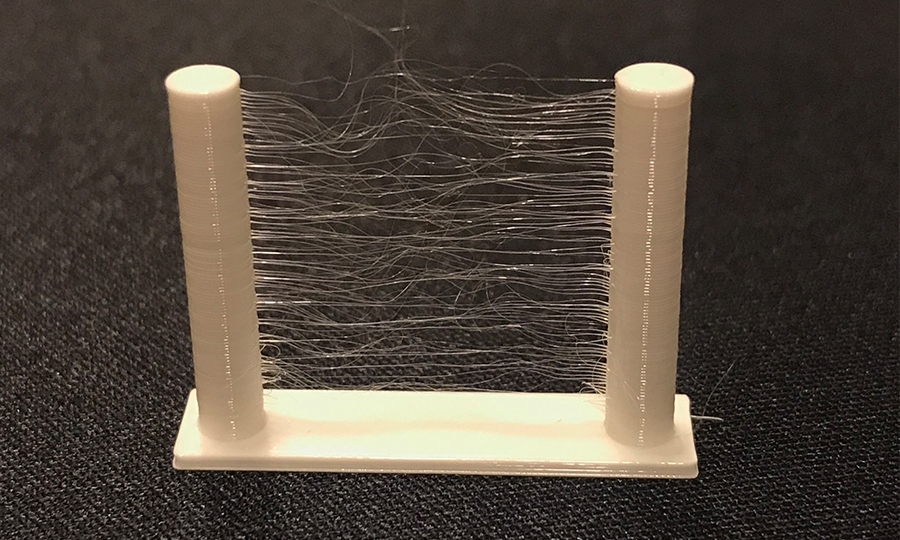
How do I solve it?
Keep the filament dry.
Stringing in 3D printing can be caused by the filament absorbing moisture, particularly in materials such as TPU and nylon. When the filament is heated in the hot nozzle during the printing process, the moisture stored in the plastic turns into steam, which can displace the plastic out of the nozzle. As the print head moves between different parts of a print, this displaced plastic can create thin, hair-like lines known as “stringing.”
To prevent this issue, it is crucial to keep the filament dry. One method of doing this is by storing the filament in an airtight container with a moisture-absorbent material such as silica gel. This will help prevent moisture from entering the filament and causing stringing during the printing process. It is also recommended to keep the filament in a cool, dry place and to avoid opening the filament container until the filament is ready to be used.
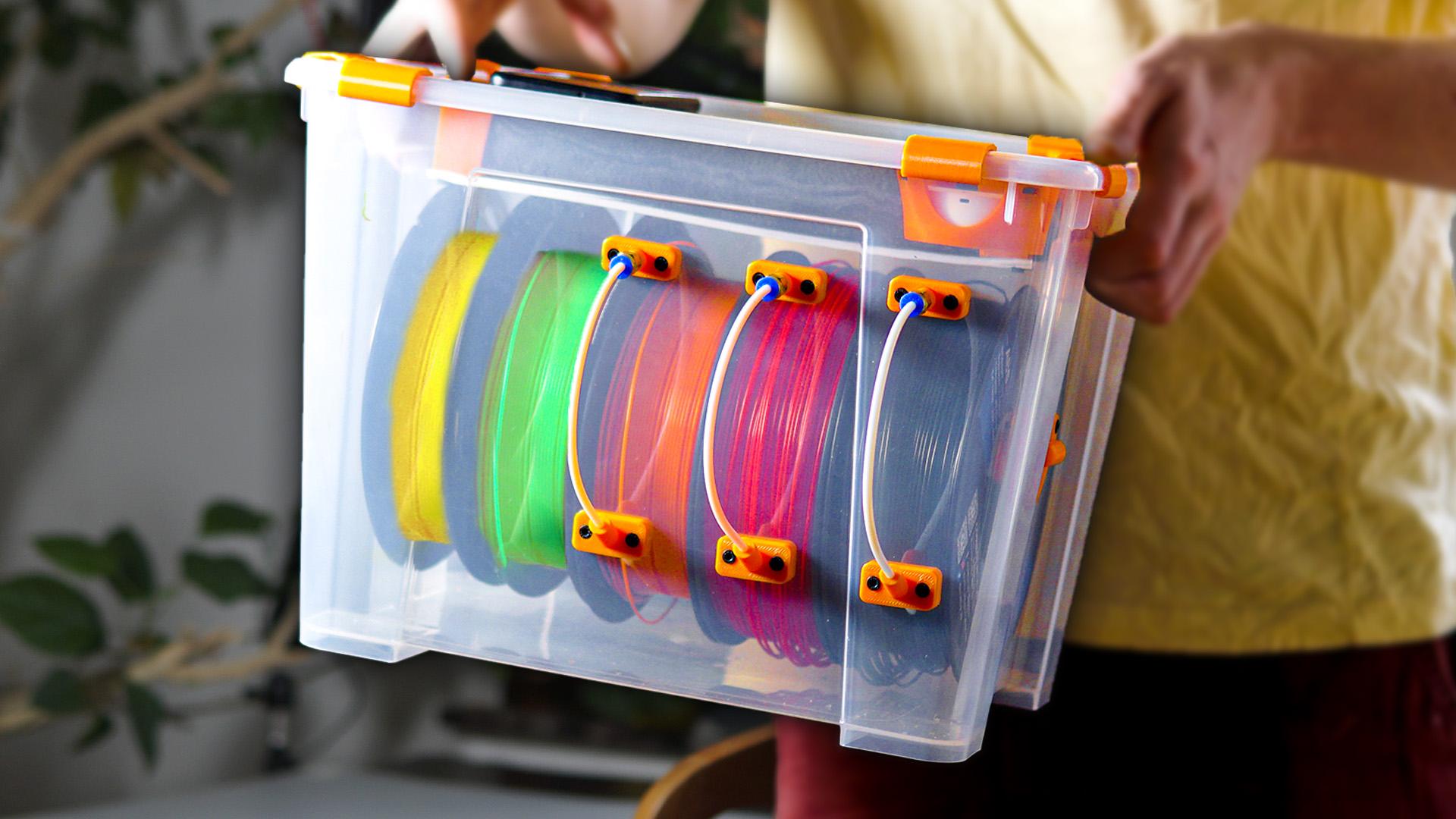
Use retraction settings.
During 3D printing, the extruder pushes the filament into the hot end, where it melts and is then forced through the nozzle opening to create the desired object. However, when the object being printed consists of multiple parts with spaces in between, the print head needs to move between these parts in order to continue the extrusion process.
As the print head moves through these empty spaces, the extruder stops pushing the filament, allowing molten filament to leak or ooze out of the nozzle, forming thin, hair–like lines known as stringing.
To counter this problem, many 3D printers have a retraction setting that can be adjusted in the slicer software. When activated, this setting causes the extruder to pull the filament back as the print head moves from one point to another, thereby reducing the amount of filament leaking from the nozzle. This can be done by adjusting the retraction distance (the distance at which the filament is pulled back) and retraction speed (the speed at which it is pulled back). By properly adjusting these settings, it is possible to minimize stringing and achieve a cleaner and more precise print.
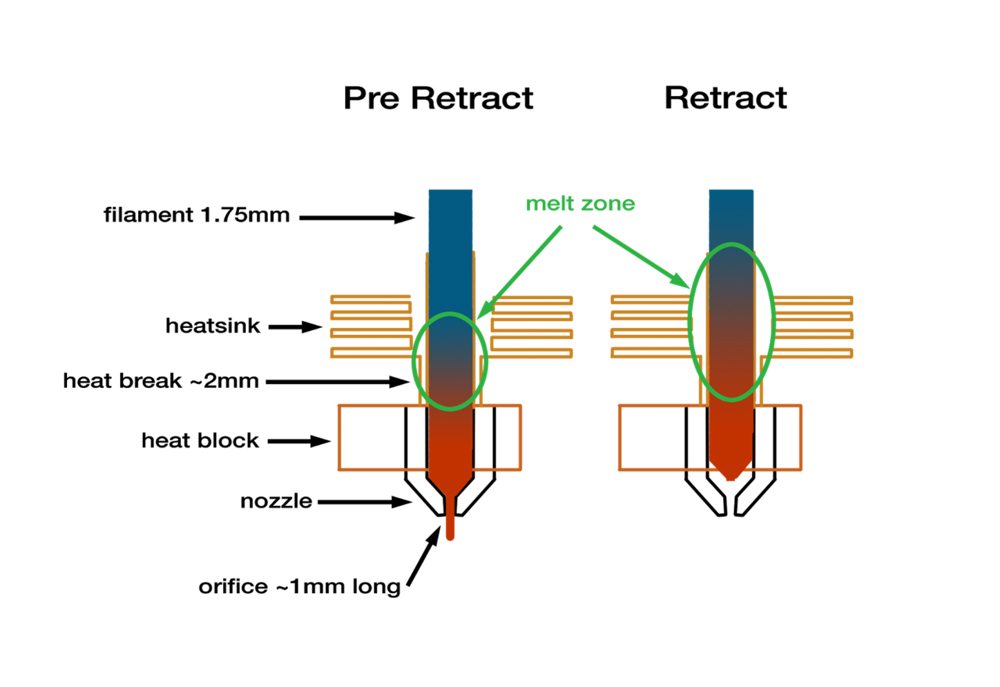
Retraction distance
Retraction distance is a crucial setting in 3D printing that refers to the distance the filament is pulled back from the nozzle opening during the retraction process. To ensure a successful print, this setting must be precisely adjusted. If the retraction distance is set too low, stringing may occur. On the other hand, if the retraction distance is set too high, the filament may not be fully extruded before the print head moves to the next point, resulting in under-extrusion or poor layer adhesion.
Determining the optimal retraction distance requires testing different settings and observing the results. These tests should be conducted using the specific filament and printer that will be used for the final print. The appropriate retraction distance can vary significantly depending on factors such as filament type, temperature, and other print settings.
Retraction speed
Retraction speed is a setting in 3D printing that refers to the speed at which the filament is pulled back during the retraction process. It is an important setting that affects the final print quality. The appropriate retraction speed can vary depending on the type of filament being used, the temperature, and other variables. To determine the appropriate retraction speed, it is necessary to conduct multiple tests using different speeds and observe the results. These tests should be done using the specific filament and printer that will be used for the final print.
Retraction speed is usually set between 40 and 60 mm/s, but this can vary depending on the filament type and other factors. For example, if the filament is prone to stringing, a higher retraction speed may be needed to pull the filament back faster and prevent stringing. On the other hand, if the filament is prone to jamming, a lower retraction speed may be needed to prevent the filament from being pulled back too fast and causing jamming. It is important to find the right balance between retraction distance, retraction speed, and other settings to achieve the best print quality.
Print at the right temperature
The temperature at which the filament is printed can have a significant impact on the final print quality and the likelihood of stringing. When the temperature is set too high, the viscosity of the molten filament decreases, making it more prone to leaking or oozing out of the nozzle and creating stringing. On the other hand, when the temperature is set too low, the filament may not melt properly, leading to problems such as under-extrusion and poor layer adhesion.
For most filaments, the recommended printing temperature range is between 190-225°C. However, to achieve the best print quality and minimize the likelihood of stringing, it is ideal to print within a narrower range within this range. For example, if the filament printing temperature range is 190-225°C, a proper printing temperature without stringing could be 200-210°C.
It is important to note that the appropriate printing temperature can vary depending on the filament type, the printer, and the printing conditions. Therefore, it is recommended to conduct tests to determine the optimal printing temperature for the specific filament and printer being used. This can be done by adjusting the temperature incrementally and observing the results to see which temperature produces the best print quality and minimizes stringing.
printing speed
The relationship between temperature and speed during 3D printing is complex, with each affecting the other in various ways. When the temperature is set too low, the filament may not melt properly, leading to problems such as under-extrusion and poor layer adhesion. In this case, it is preferable to reduce the printing speed, this will allow the plastic more time to gain the heat necessary for melting through the nozzle and ensuring proper extrusion.
On the other hand, when the temperature is set too high, the viscosity of the molten filament decreases, making it more prone to leaking or oozing out of the nozzle and creating stringing. In this case, it is preferable to increase the printing speed, this will help to prevent the plastic from gaining too much heat and minimize the chances of stringing.
To achieve the best print quality, it is important to find the right balance between temperature and speed. This balance can vary depending on the filament type, the printer, and the printing conditions, therefore it is recommended to conduct tests to determine the optimal temperature and speed for the specific filament and printer being used. This can be done by adjusting the temperature and speed incrementally and observing the results to see which combination produces the best print quality and minimizes stringing.
Use a direct-drive extrusion system
The type of extrusion system used in a 3D printer can have a significant impact on the likelihood of stringing. There are two main types of extrusion systems: Direct Drive and Bowden tube.
In a Direct Drive extrusion system, the extruder is located directly above the hot end on the x-axis. This allows the filament to be extruded directly to the hot end through a very short distance, resulting in a tight movement of retraction and extrusion. This tight movement helps to minimize the likelihood of stringing.
On the other hand, in a Bowden tube extrusion system, the extruder is fixed on the printer frame and pushes the filament to the hot end through a Bowden tube. Due to the distance between the extruder and the hot end in this system, the movement of retraction and extrusion is less tight, which can result in increased flexibility and a greater likelihood of stringing. To compensate for this increased flexibility, a greater retraction distance is often required.
In summary, Direct Drive extrusion systems are less prone to stringing as the distance between the extruder and the hot end is short, allowing for a tight movement of retraction and extrusion. While Bowden tube extrusion systems have a greater distance between the extruder and the hot end, which can result in increased flexibility, therefore, a greater retraction distance is required to minimize the likelihood of stringing.
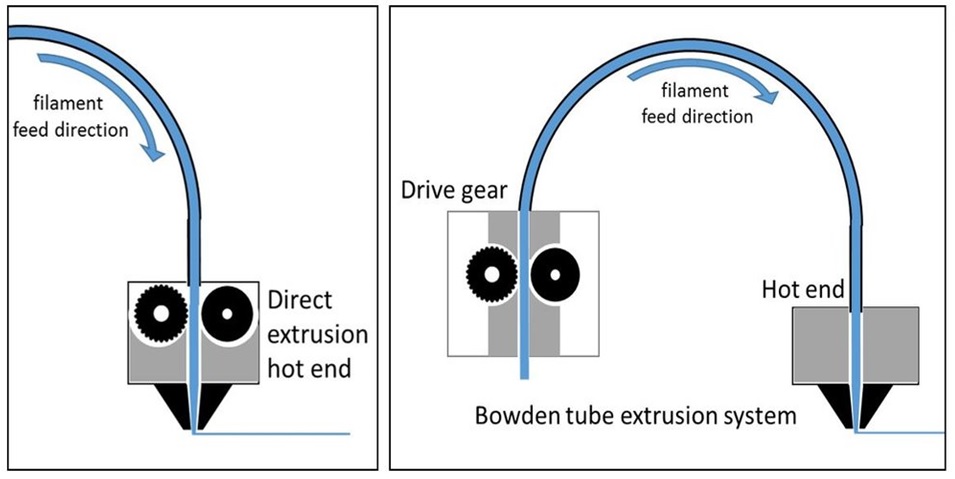
Enable z-hop
Z-hop is a technique used in 3D printing that involves the nozzle rising slightly above the printed part before moving to another point. Its primary benefit is to prevent the nozzle from hitting the printed part, which can cause damage and affect the final print quality. However, it has also been observed that Z-hop has a limited effect in reducing stringing.
The reason for this is that when the nozzle rises slightly above the printed part, it prevents friction between the nozzle and the plastic, which reduces the chances of the plastic sticking to the hot nozzle and melting. This can help to minimize the likelihood of stringing, however, the effect is limited as stringing can also occur due to other factors such as temperature, retraction settings, and the type of extrusion system used.
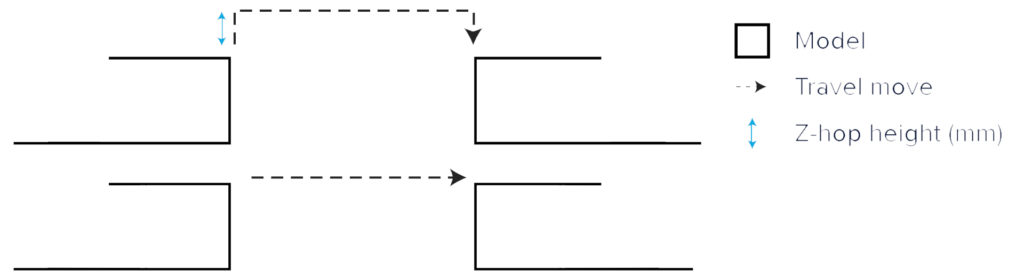
In summary, while Z-hop can be an effective technique to prevent the nozzle from hitting the printed part, its effect on reducing stringing is limited. To minimize the likelihood of stringing, it is important to consider other factors such as temperature, retraction settings, and the type of extrusion system used. Additionally, it is important to conduct tests to find the optimal settings for a specific filament and printer.