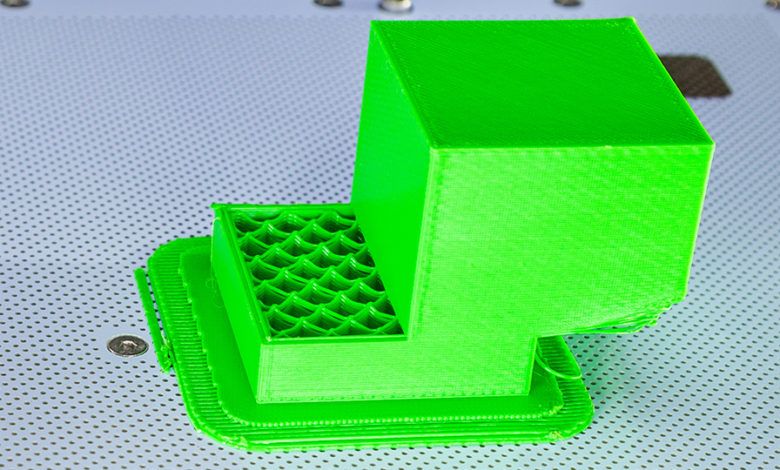
What is layer shifting?
Layer shifting is a common issue faced by users of FDM 3D printers, causing damage to the entire printed object, and wasting time and filament. The problem occurs when the printer head moves to an incorrect location during the printing process and continues to print, creating a distortion in the design. It is caused by a misalignment of the layers that form the printed object, which is a result of various factors such as mechanical problems, printing settings, and electronic component issues. It can be a frustrating experience for users and can lead to significant losses in terms of time and resources.
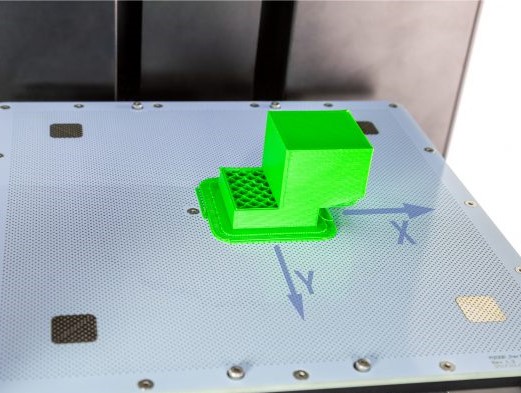
What are the causes of 3d printing layer shifting?
Layer shifting can be caused by a variety of factors. These include mechanical issues such as loose timing pulleys or belts, an unstable build plate, or electronic issues such as overheating components or incorrect stepper motor voltage/current. Additionally, it can be caused by improper printing settings such as printing at too high of a speed or incorrect slicing settings. To prevent layer shifting it is important to identify and address the specific cause of the problem.
Mechanical issues:
Timing pulleys
In a 3D printer, the movement of the print head in the x and y axes is controlled by a pulley that is attached to the motor shaft. The pulley then transmits the movement to the timing belts which are connected to the x and y-axis elements. The pulley is held in place by a grub screw, which ensures that it rotates together with the motor shaft. If the grub screw is loose or not tightened properly, the pulley will not rotate correctly with the motor shaft, resulting in skipped steps and ultimately causing layer shifting. To prevent this, it is important to regularly check and tighten the grub screw.
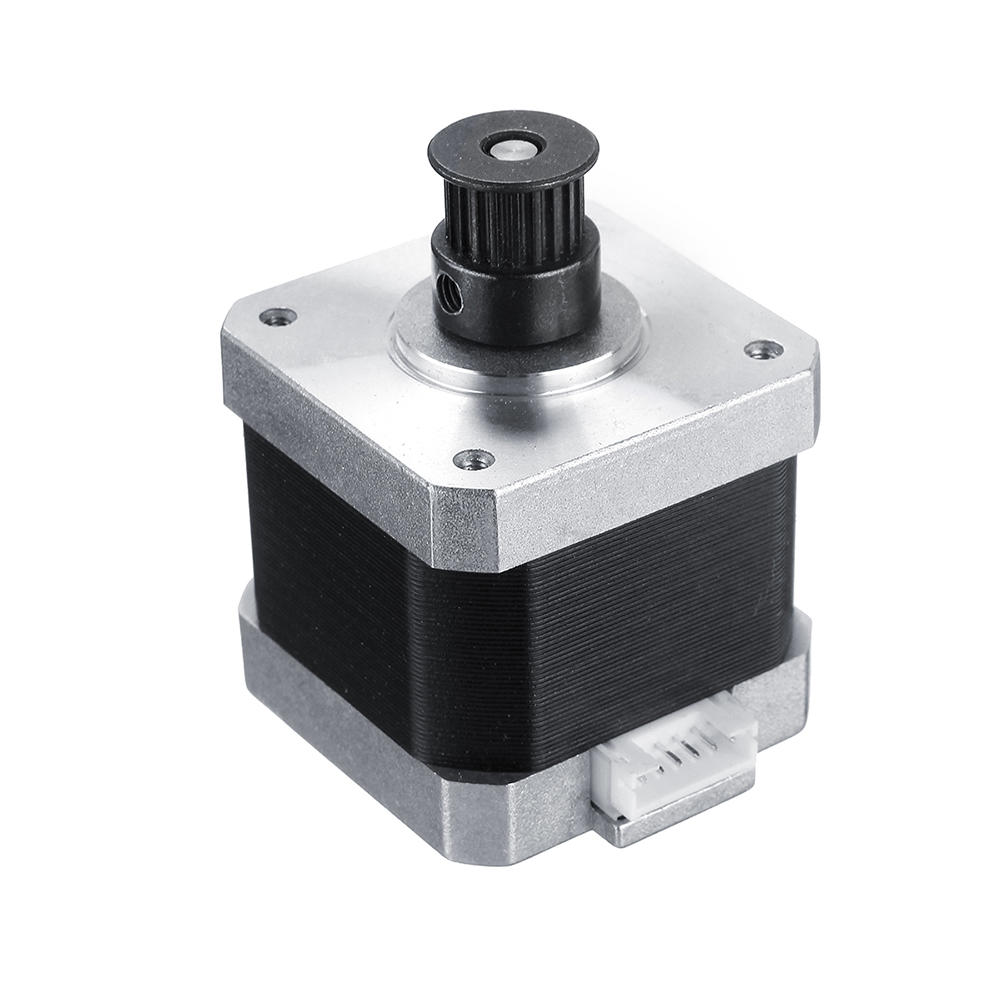
Timing belts
The timing belt in a 3D printer is responsible for transmitting the movement of the print head in the x and y axes. If the belt is too loose, it will not grip the timing pulley properly and will cause the movement to be transmitted incorrectly, resulting in layer shifting. On the other hand, overtightening the belt will cause excessive friction and wear on the idler pulley bearing, the stepper motor shaft, and the internal bearing. This will cause the belt to stretch and the fibers to be damaged over time, which may require the belt to be replaced. To prevent this, it is important to ensure the belt is tight enough so that it is not too loose or too tight and to check the belt tension regularly.
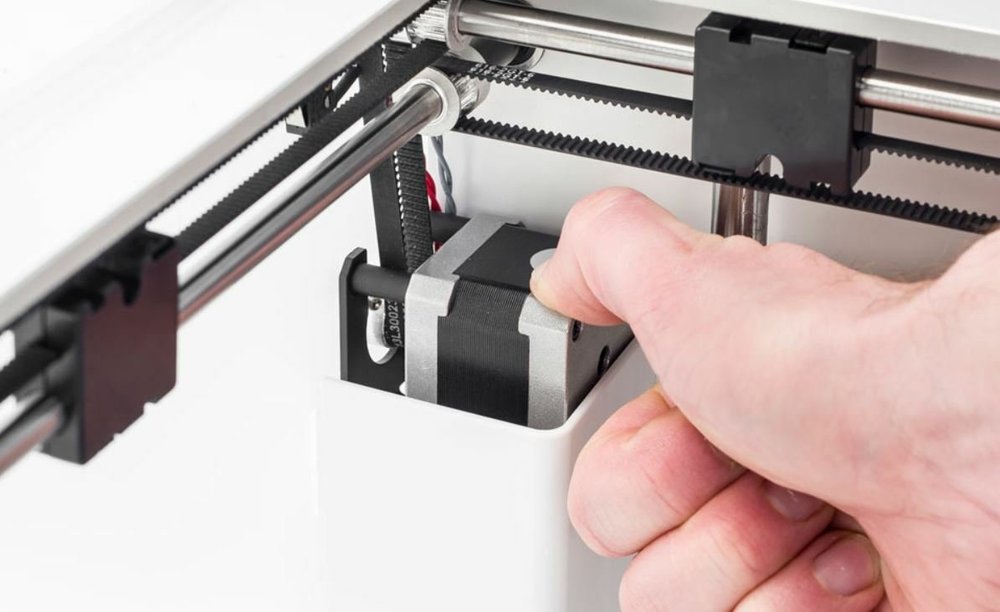
Build plate
In a Cartesian 3D printer mechanism, the build plate moves back and forth during the printing process. If the build plate is not stable enough, it can cause the printed object to shift or move during the printing process, leading to layer shifting.
To prevent this, it is important to ensure that the build plate is properly secured to the printer. This can be done by using binder clips or other suitable means to fix the printing surface to the build plate. This will ensure that the build plate remains stable throughout the printing process, preventing any movement or shifting of the printed object. Additionally, it is important to ensure that the build plate is level and that it is clean and free of any debris before starting the print. This will also help to ensure a stable printing surface and prevent layer shifting.
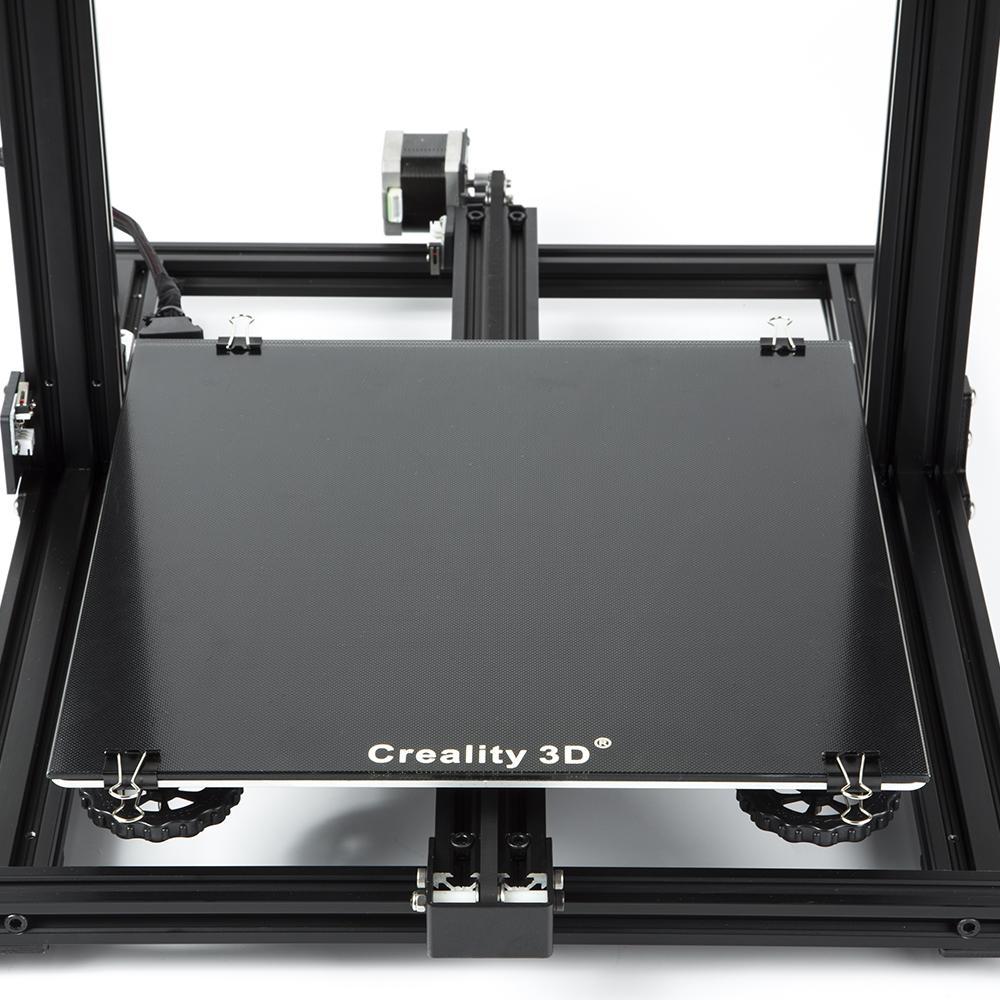
Electrical/electronic issues:
Cooling of electronic components
If no mechanical issues are found, it is likely that the problem is related to electronic components. Overheating of the control board and stepper motor drivers can lead to layer shifting.
To prevent this, it is important to ensure proper cooling of the electronic components. One way to do this is by installing an external cooling fan. This will help to dissipate heat away from the control board and stepper motor drivers, preventing them from overheating. Additionally, proper ventilation of the printer should be maintained to ensure that the air circulation inside the printer is good and the heat generated by the components is dissipated properly. This will help to reduce the risk of overheating and prevent issues such as layer shifting. It’s also important to check the power supply and the fuses to make sure they are not causing any overheating issues.
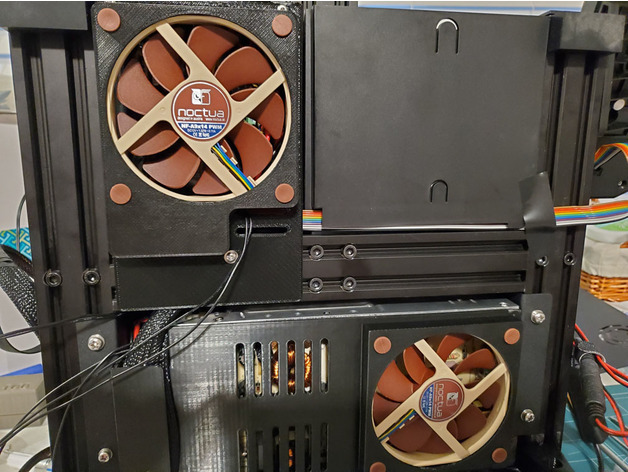
Stepper motor voltage/current
Adjusting the stepper motor’s VREF (Voltage Reference) is an important step in preventing layer shifting. VREF controls the amount of current that is provided to the stepper motor, and the optimal setting will vary depending on the type of stepper motor that is being used. A decrease in current will cause the motor to skip steps during printing, which can result in layer shifting. On the other hand, delivering too much current to the motors can cause them to overheat, which can also lead to layer shifting.
To prevent these issues, it is important to adjust the VREF setting to the correct level for the specific stepper motor that is being used. This can typically be done by adjusting a screw or pot on the stepper motor driver. It is also important to check the power supply, to ensure that it is providing the correct voltage and current to the stepper motor. Additionally, regular maintenance of the stepper motor and the driver is necessary to avoid overheating or other issues that might cause layer shifting.
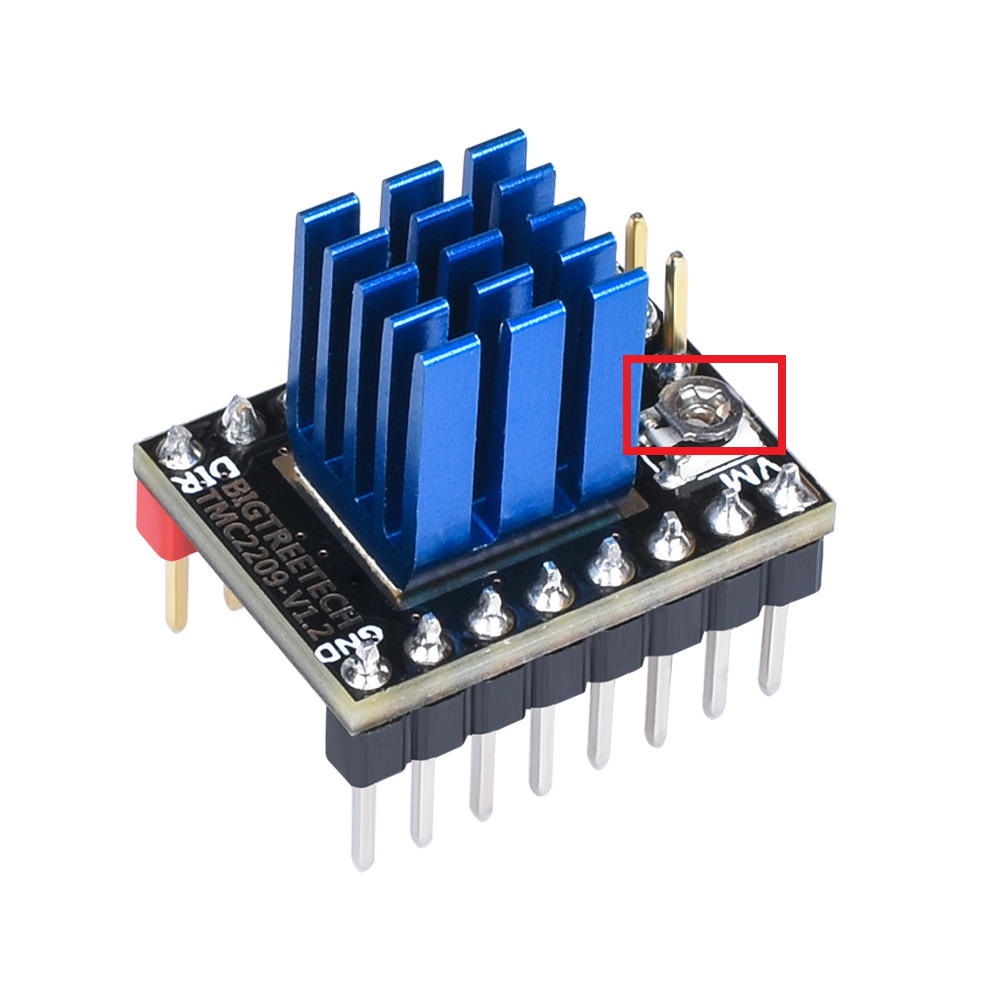
Print setting:
Print speed
Too high a printing speed can cause layer shifting due to mechanical reasons or electrical limitations.
With regard to electrical limitations, if the printing speed is too fast, the control board’s processor and motor drivers will be unable to process the signals associated with the high speed in time. It is also possible that high speeds are greater than the stepper motor’s ability to handle, this leads to layer shifting occurring repeatedly.
And when it comes to mechanical causes, regardless of the printer’s mechanism, when printing is very fast and with rapid and sudden movements of the printer’s moving parts in the x and y axes, the inertia force of the moving parts becomes large. This force may be greater than the torque that the stepper motor can withstand, or it may cause the belts to slip on the pulleys, resulting in layer shifting.
It is recommended to set the print speed and travel speed to be within acceptable limits.
Enable Z-hop setting
This means that the nozzle will rise slightly above the printed part before moving to another point. Its main benefit is to prevent hitting the printed part.
Sometimes when the print head moves from one point to another, a collision occurs between the nozzle and the top of the design. This collision may cause two problems
A- The part being printed is shifted from its position, which causes layer shifting.
B- If the design adheres well to the build plate and is not shifted by impact, the belt can slip on pulleys and also lead to layer shifting as a result of high-speed movement.
Although these collisions don’t happen very often, activating z-hop prevents this problem and is generally useful anyway.
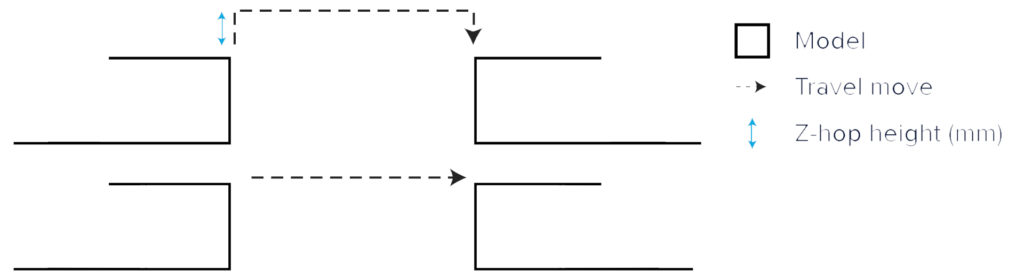