Achieving Reliable 3D Prints: Design Tips for Engineering Materials
Strengthening Your Design with Ribs
Introduction
As 3D printing technology continues to evolve, its applications have expanded beyond prototyping and artistic creations to include engineering-grade materials. However, working with these materials presents unique challenges, such as higher shrinkage tendencies leading to warping. To overcome these obstacles and achieve reliable 3D prints, it is essential to optimize the design of your models. In this article, we will explore essential design guidelines and features to consider when creating 3D printed parts with engineering materials.
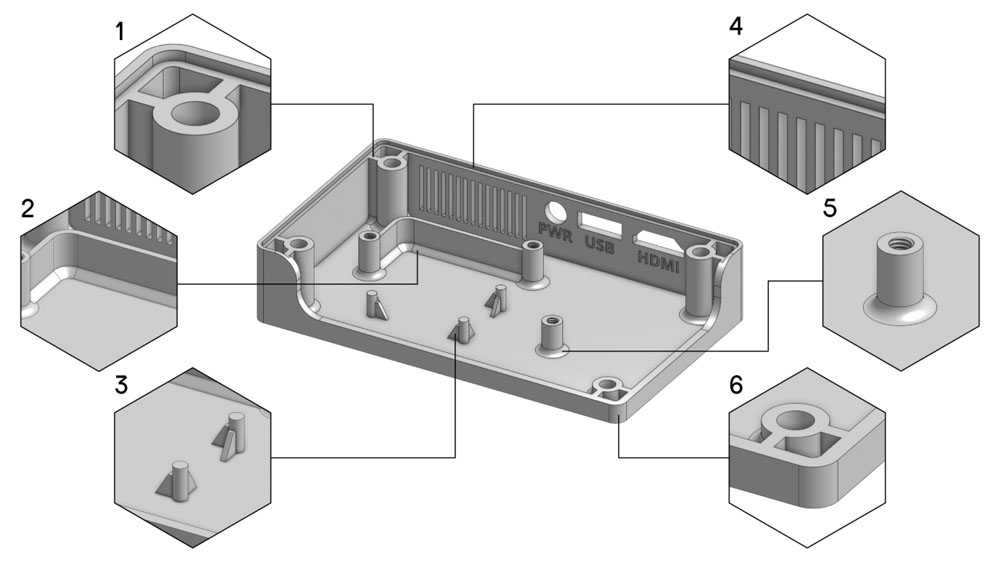
printed parts
- Rib
- Chamfer
- Gusset
- Wall thickness
- Fillet
- Rounded corners
Strengthening Your Design with Ribs
Ribs are fundamental features for enhancing the structural integrity of your 3D printed parts. They involve adding a specific thickness of material in a designated direction between the contour and an existing part. Not only do ribs connect the part to a wall, but they also offer additional support from the bottom surface. By incorporating ribs strategically, you can make your 3D printed parts stronger and less prone to deformation during printing.
Reducing Stress with Chamfers
Chamfers play a crucial role in ensuring successful 3D prints. They are beveled edges or corners added to the design to reduce stress points. When sharp corners are avoided, stress accumulation during the printing process is minimized. As a result, chamfers contribute to producing more reliable and robust 3D printed parts.
Supporting with Gussets
Gussets provide valuable support to features of a 3D printed part from the bottom surface. Unlike ribs, gussets taper off as the height of the part increases. By incorporating gussets in your design, you can effectively strengthen delicate areas and maintain stability during printing, even with challenging engineering materials.
Uniform Wall Thickness for Stability
Maintaining a uniform and consistent wall thickness throughout the model is one of the most critical design considerations for 3D printed parts. Having a consistent wall thickness reduces the likelihood of warping or shrinkage during printing. By ensuring that all sections of the part have equal wall thickness, you can achieve better overall stability in your 3D prints.
Stress Reduction with Fillets
Fillets are designed to reduce stress points in a 3D printed part. They achieve this by creating smooth, rounded transitions between different surfaces. As stress accumulates during the printing process, fillets play a crucial role in minimizing these concentrations and promoting higher print quality.
Benefits of Rounded Corners
using rounded corners in your 3D printed part design helps distribute stress more evenly throughout the material. This even distribution of stress enhances the overall print quality and reduces the risk of weak points or fractures. Rounded corners are particularly beneficial when using engineering materials, as they ensure better structural integrity in the final printed part.
Layer Height:
Choosing an appropriate layer height is crucial when printing with engineering materials. A smaller layer height can improve the overall surface finish and detail resolution of the printed part, but it may also increase print time. Conversely, a larger layer height can reduce print time but may result in a coarser surface finish. Finding the right balance between print quality and speed is essential.
Infill Density:
Adjusting the infill density can significantly impact the mechanical properties of the printed part. Higher infill densities provide increased strength and rigidity, making the part suitable for load-bearing applications. On the other hand, lower infill densities reduce material usage and print time, making them more cost-effective for non-structural parts.
Print Speed:
Controlling the print speed is essential when working with engineering materials. Printing too quickly can lead to overheating and deformation of the material, while printing too slowly may cause issues like oozing or stringing. Finding the optimal print speed for each material is essential for achieving successful prints.
Conclusion
When designing 3D printed parts using engineering materials, adhering to specific guidelines and incorporating the mentioned features is crucial for success. Ribs, chamfers, gussets, uniform wall thickness, fillets, and rounded corners all contribute to improving the structural integrity and reliability of your 3D prints. By carefully considering these design guidelines, you can confidently create 3D printed parts that meet the highest standards of functionality and durability. Additionally, by following the design recommendations for challenging engineering materials, you can further enhance the quality and success rate of your prints. 3D printing with engineering materials opens up a world of possibilities for creating robust and functional parts, and with the right design approach, you can unlock its full potential.